The Importance of CNC Precision Machining in Modern Manufacturing
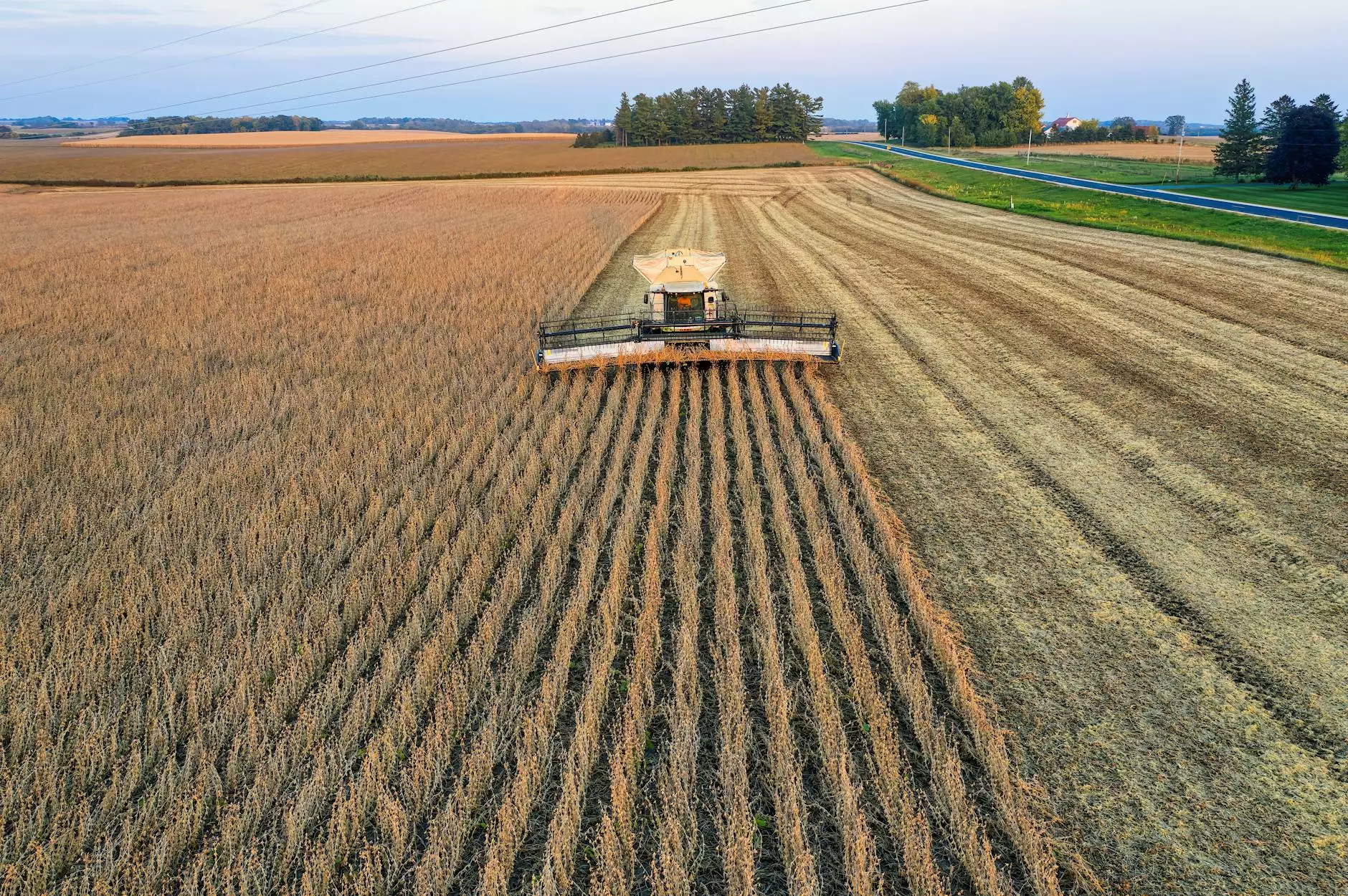
In today's world of advanced manufacturing, CNC precision machining factories play a pivotal role. As industries evolve, the demand for precision and efficiency in production processes has skyrocketed. CNC, which stands for Computer Numerical Control, utilizes computer systems to automate the control of machinery, leading to consistent and high-quality output. This technology has transformed traditional metal fabrication into a more refined and accurate process.
What is CNC Precision Machining?
CNC precision machining is a manufacturing process that involves the use of computer-controlled machines to create parts and components from various materials. This process can include drilling, milling, turning, and grinding, allowing manufacturers to produce complex shapes and intricate designs with remarkable accuracy.
Why Choose a CNC Precision Machining Factory?
When a business requires detailed designs and reliable production, partnering with a CNC precision machining factory can offer numerous benefits. Here are several reasons why companies prefer CNC precision machining:
- Unmatched Accuracy: CNC machines can produce parts with tolerances of less than a thousandth of an inch, ensuring that each component meets precise specifications.
- Repeatability: Once programmed, CNC machines can produce any number of identical parts without variation, which is vital for large-scale production.
- Complex Geometries: CNC machining enables the creation of complex geometries that would be impossible or impractical with traditional manufacturing methods.
- Reduced Lead Time: The automation of processes reduces the time taken to produce each component, speeding up the overall manufacturing processes.
- Material Versatility: CNC machines can work with a wide range of materials, including metals, plastics, and composites.
The Role of Metal Fabricators in CNC Precision Machining
Metal fabricators are essential to the CNC precision machining landscape. They provide the foundational processes that lead to precise and durable components. Here’s an overview of how metal fabricators contribute:
- Material Selection: Skilled fabricators understand the properties of various metals and can recommend the best material for each specific application.
- Preparation of Materials: Fabricators often perform preliminary processes such as cutting, punching, or bending before CNC machining, ensuring the material is ready for precision work.
- Quality Assurance: Metal fabricators implement stringent quality control measures to ensure that all components meet industry standards and client expectations.
The Process of CNC Precision Machining
Understanding the steps involved in the CNC precision machining process can provide insights into its effectiveness and efficiency. Here is a typical workflow:
- Design: Engineers create a detailed CAD (Computer-Aided Design) model of the component, which serves as the blueprint for machining.
- Programming: The CAD model is converted into G-code, a language that CNC machines understand, dictating their movements and actions.
- Setup: Operators set up the CNC machine, ensuring that tools and materials are in place for production.
- Machining: The CNC machine executes the programmed instructions, cutting and shaping the material into the desired part.
- Inspection: Finally, the finished component is inspected for quality and accuracy, ensuring it meets the required specifications.
Advantages of Using Deep Mould for CNC Precision Machining
Deep Mould, one of the premier CNC precision machining factories, epitomizes excellence in metal fabrication. Here’s why partnering with Deep Mould provides unparalleled advantages:
- State-of-the-Art Technology: Deep Mould invests in cutting-edge CNC machinery, allowing for unparalleled precision and efficiency.
- Experienced Team: The team at Deep Mould consists of seasoned professionals with extensive experience in metal fabrication and CNC machining.
- Custom Solutions: Whether you need one-off parts or mass production, Deep Mould offers tailored solutions to meet your specific requirements.
- Commitment to Quality: With strict quality control protocols, Deep Mould ensures every machined component meets the highest standards.
- Sustainable Practices: Deep Mould is committed to environmentally friendly manufacturing practices, reducing waste and optimizing resource usage.
Understanding the Applications of CNC Precision Machining
CNC precision machining has a wide array of applications across various industries. Understanding these applications can highlight the versatility and importance of CNC technology:
- Aerospace: CNC machining is crucial in the aerospace industry for manufacturing components that require stringent safety and precision standards.
- Automotive: Automotive manufacturers rely on CNC machining to produce complex engine components, transmission systems, and chassis parts.
- Medical Devices: The medical industry uses CNC machining to produce surgical instruments and implantable devices that must meet strict health standards.
- Electronics: Precision machining is vital for creating parts in computers, smartphones, and other electronic devices, ensuring small and intricate components are accurately made.
- Industrial Equipment: CNC technology is used to fabricate machinery components and tools that require high precision.
Future Trends in CNC Precision Machining
As we move further into the 21st century, several trends are shaping the future of CNC precision machining. Keeping an eye on these trends is vital for businesses looking to stay ahead:
- Automation and AI: The integration of artificial intelligence and automation systems into CNC machining is revolutionizing efficiency and productivity.
- Increased Customization: With advancements in technology, the ability to customize parts on-demand is becoming easier, allowing for more personalized manufacturing solutions.
- 3D Printing Hybrid Technologies: The combination of CNC machining with 3D printing is opening new doors for manufacturing complex parts that would have been impossible to create before.
- IoT Integration: The Internet of Things is enabling real-time monitoring of CNC machines, improving maintenance and reducing downtime.
- Sustainability Efforts: Manufacturers are increasingly focusing on sustainable practices, including recycling materials and reducing energy consumption.
Conclusion: The Future of CNC Precision Machining with Deep Mould
In conclusion, the role of CNC precision machining factories like Deep Mould is more critical than ever, encompassing precision, efficiency, and the adaptability required in today’s fast-paced manufacturing environment. By harnessing advanced technology, skilled personnel, and sustainable practices, Deep Mould leads the way in delivering high-quality metal fabrication solutions.
Don’t compromise when it comes to quality—choose Deep Mould as your CNC precision machining partner, where excellence is not just a goal, but a guarantee.